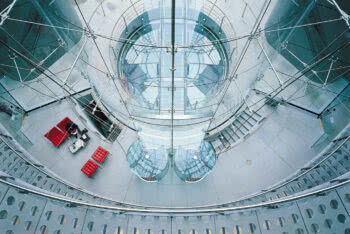
What Building Products Manufacturers Need to Know About Smart Buildings
By Maria Lester, LEED AP
The building construction industry touches every part of our lives – from our homes, schools and workplaces, to our community spaces and general infrastructure. Beyond doubt, connecting the technology infrastructure to the physical spaces and buildings where we work and live can deliver significant benefits – managing the use of energy, optimizing space utilization, and controlling operational and maintenance costs among them.
When you think of how technology has reshaped the building construction industry, new construction usually comes to mind first. While technology can improve the design and construction process, implementation of technology must be part of a broader strategic platform.
However, newly built intelligent buildings represent a tiny fraction of the built space. Existing buildings far outnumber any new construction. Statistics show that for every new commercial property being built, there are approximately 100 existing buildings of a similar type. Considering all building types, the numbers become staggering. According to IFMA (International Facilities Management Association), one in every three buildings is more than 50 years old. More than 70% of buildings are 20 years old, or older!
It is safe to assume that these existing buildings overall are not “smart” and accessing information about any aspect of them is difficult and in many cases, cost prohibitive. The majority still operate the same way they did decades ago. Even though new technologies have been emerging at a rapid pace, it is challenging to transition these buildings into the digital world where they need to operate.
Whether dealing with new construction or retrofit, managing a “smart” building changes everything. And yet, the facilities management industry is no stranger to technology. It has been using computer-based tools for decades, although most of the technology in use is now dated[1]. Even so, these solutions are often proprietary in nature, information is server-based, and most importantly, it lacks instant access.
What is Smart?
The transition to smart buildings has become much more than energy efficiency. IoT and mobile technology are the game changers, escalating the technology transition and leading to improved communication, on-site access to computing functionality, and accurate data recording. In other words, everything in the building is getting “smart.”
The goal however remains the same: to have solutions that will ensure healthy building and infrastructure operations while also reducing costs, improving productivity and boosting sustainability.
According to Konkana Khaund, Director of Consulting Energy, Buildings & Smart Infrastructure at Frost & Sullivan, the challenge is not technology—it is here and it is proven—but, rather, it is the willingness and preparation to take advantage of it[2].
For example, retrofitting an existing building requires weaving “smart” technology into the existing infrastructure, including WiFi, ethernet, Bluetooth mesh and smart sensors. Once the “smart” infrastructure is developed, a retrofitted “smart” building can return all the same benefits of a newly built “smart” building.
The New Standard: Integrated Smart Systems
Monitoring and managing building conditions has always been a time-intensive job for the facilities management team, so the rise of the “smart” building is a positive development. Failures of equipment, even the smallest component, can really hurt a building’s profitability, so preventing problems is one of the most important jobs for any facilities manager.
“Smart” systems have changed and are changing the way building information is accessed. Not just information related to building use or occupation, but also critical information for emergency, safety, compliance and the day-to-day functions of building operations and maintenance are being affected. It is vital not only to the operation of a building, but to occupants’ well-being and the growth of an organization.
“The goal is to have more measurable output to evaluate performance,” says Khaund. “Automation provides more tangible output and intelligence. Building management companies use automation to get data and output for trend information, navigate investments, where to cut costs, where to be more efficient and to predict operations.”[3]
For example, the use of apps is transforming the job of facilities managers regardless of the age of the building or the sophistication of its systems. Facilities managers can get instant access to any building-related information being electronically monitored, not only to prevent accidents from becoming catastrophes, but also to reduce operating costs and significantly improving customer service. Plus, when problems arise at a building, action can be taken in real-time using a “smart” device.
“Many of the big facility management companies have their own platforms that work with manufactures to customize products/software to optimize the operation of the buildings they manage. These systems operate to maximize efficiencies in many building services areas including energy, security, maintenance and even cyber security,” Khaund explains.[4]
The ability of building products to be “smart” and to communicate in real-time is crucial. This is true not only during renovation, but also in new construction. For example, using the cloud is all well and good, according to people who study these techniques, but the real key is integration. It does no one any good if systems can’t talk to each other, especially if real-time data is required. Diverse systems create problems. Even within similar systems, variations or home-grown software add-ons create a multitude of issues for true integration.
And yet, such integration exposes the enterprise to cyber attacks. When you have layers of software, and you break one layer, it’s more difficult to get to another one. However, if they are all operating under a single platform, cracking in opens the entire system to havoc. This is only increased when you have devices talking to each other to not only devices within the facility, but to devices outside the facility.
What’s in Your Product?
Manufacturing is no longer simply about making physical products for buildings. The idea of standalone building products working in isolation is quickly becoming a thing of the past. Smart and connected devices are the foundation of the IoT. In other words, smart buildings require products to have technology that will support integration into a building’s network (IoT)[5].
In short, the building becomes the product.
But, what does that mean for a building products manufacturer?
We can learn from the first product adapters of a “smart” building, whether new constriction or retrofit. Thanks to IoT, the products within a building that we interact with daily – security, lights, sensors, windows, HVAC units, doors and CCTV — are being transformed from mere static, standalone forms to objects with cognition.
It’s that idea of cognition that changes everything.
Sensors can be used to recognize context and circumstance and then adapt the way they work accordingly[6]. These sensors then communicate in real-time with facility managers. Notifications can also be communicated through programmed mobile apps.
For example, consider today’s HVAC products that can use their cognition (sensor) to work more efficiently, more effectively and more intuitively than has ever been possible before. The combination of IoT and HVAC systems sees several different wireless sensors, smart vents and other technologies come together and add intelligence that helps the two communicate.
Adding sensors and connectivity are the first steps in turning “dumb” products into “smart” ones, thereby giving the building more thinking power. By harnessing the power of IoT, the network of everyday objects is equipped with sensors that can record, send, and receive data over the Internet without human intervention, putting the building to work for us, including providing optimal lighting, heating and temperature without any user input, as well as save money and reduce environmental impact.
It’s About the Information, Stupid
Any building product that needs monitoring and maintenance should include a form of product-monitoring technology that can capture and transmit key data such as maintenance issues, early warnings or vital signs in real time or near-real time.
Why? Because everything in the building is an asset, and asset management is what monitoring is all about. In other words, it’s the information that the products produce that become the asset[7].
Think about your body. Your body has components in it (heart, liver, etc.). But, it’s the information from the components that tell you the health of your body.
The same is true of a building’s health, only the components are the assets – things like lighting, duct systems, plumbing products. The nerve center of a building manages the information from these components, like your brain manages information from the body’s components. “Manufacturers of building industry products need to create more scalable solutions,” explains Khaund. “Plus make the product inventory process less complex for products to move correctly and smoothly through the value chain into the final process of installation, considering the numerous entities and touch points it navigates through along that process. Too many SKUs can confuse a system.”[8] Having components talk to each other requires standardization – and as a manufacturer, one of the things you strive for is non-standardization. You don’t strive to have your components talk to a competitor’s component.
But, if you are interested in the building as the product itself, you have to. Systems need to talk to each other and work together for the entire building to maximize success. Integration is and always will be the key.
At the end of the day, keeping it simple is really the answer. While technology is a central part of designing and manufacturing “smart” connected products, the core feature/function still needs to be central to a “smart” connected device with the idea that the building is the product[9]. Do not get distracted by this connected benefit because at the end of the day it still needs to work and be a seamless experience.
_________________________________________________
References
[1] In a recent case history, a major manufacturer was using out-of-date security software. In evaluation, the software manufacturer announced he was ceasing support for that software, requiring the manufacturer to invest thousands of dollars to migrate to a new platform. The manufacturer did a best-in-class study and changed vendors. This is not an isolated case.
[2] Interview with Konkana Khaund, Director of Consulting Energy, Buildings Smart Infrastructure at Frost & Sullivan, September 17, 2019
[3] Ibid.
[4] Ibid.
[5] McKinsey has a nice paper on IoT called Making Sense of Internet of Things Platforms. In it, they noted “each Crunchbase for venture-funded IoT platforms, and you will get well over 100 hits. And that list doesn’t include many bigger technology players entering the market with IoT platforms like Microsoft, IBM, and SAP or several industrial companies with similar aspirations like GE, Bosch, and Siemens. There are IoT platforms of every shape and size. There are platforms for specific industries like commercial real estate and family health. Some focus on one type of device: for example, there are at least two platforms focused on augmented-reality headsets. Some are focused on a particular function, like manufacturing. There is an IoT platform for dogs.”
[6] This has been in development for years in many products. Smoke detectors, for example, have had the ability to detect a real fire based on repeated readings of levels of smoke, addressing false alarms which can occur depending on the size of space. Sensors in plumbing products have evolved over the years to detect users more accurately (though they still fire off due to faulty electronics).
[7] McKinsey’s Global Institute predicts IoT will have an economic impact of between $4 trillion and $11 trillion by 2025. Companies can capture value by creating new revenue streams from providing connected solutions and services to consumers and enterprises and by reducing costs in operations.
[8] Konkana Khaund interview, September, 2019.
[9] In one case, a process control valve manufacturer did a mean-time-between failure on the valves in a client’s plant. Not all the valve were his. When he presented it to the owner, the owner was so impressed he asked why he didn’t do it on all the valves? The control valve manufacturer told him he didn’t have the data for the competitor’s valves. The plant owner said, “Well, change them out to yours if you can’t get the information you need.” Needless to say, the control valve manufacturer had an excellent result either way. Remember, it’s about the information.